802 Boeing Safety and Quality Plan
Airplane Geeks Podcast - Un podcast de Airplane Geeks - Les mercredis
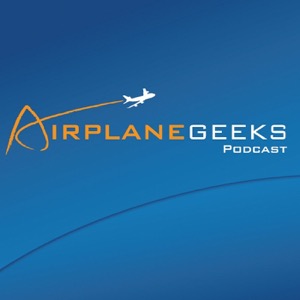
Catégories:
We take a look at the Boeing Safety and Quality Plan, the NTSB recommendations after the Southwest/FedEx near miss, the suspension of some ATC staff in India, Essential Air Service contracts, BARK Air’s lawsuit over airport-use restrictions, the sale of a B-17, and the NTSB inspection of the USAirways flight 1549 engines. Aviation News Boeing Safety & Quality Plan Boeing had 90 days to deliver a comprehensive plan to the FAA to improve the company’s safety management and quality assurance, including in the supply chain. We look at The Boeing Product Safety and Quality Plan Executive Summary [PDF, 11 pages.] The Plan includes the containment and mitigation actions Boeing took immediately after the accident. It also introduces Boeing’s new Key Performance Indicators (KPIs) of production system health and associated control limits for each KPI. Boeing intends that these metrics will provide “a continuous assessment of factory health and provide early warning of emerging quality and safety risks. They also will facilitate tracking of Boeing’s improvement under the Product Safety and Quality Plan and guide decisions about system readiness for rate increases.” Boeing's Immediate Containment and Mitigation Improvements directed at the Boeing production system: Admiral Kirkland Donald Revised the build plans, training, maintenance planning, aircraft manual documentation, removal requirements and inspection criteria for the Mid-Exit Door (MED) plug; Instituted additional controls to prevent defects in the MED plug and similar structures and assemblies; Added conformance inspections to nine critical build points; Processed fleet and production inspection findings through Boeing’s SMS and Quality Management System (QMS); Published alerts on removals and rework, signed by all factory employees; Hosted representatives from 737 airline customers to review Boeing’s production and quality procedures, and to provide feedback; Appointed a recognized safety and quality leader, Admiral Kirkland Donald, to independently assess Boeing’s production system; and Implemented a revised management and salaried compensation model focused on quality and safety, with aligned key performance indicators across all programs. Improvements directed at the Boeing supply chain: Instituted additional controls at Spirit to prevent defects in the MED plug and similar structures and assemblies; Added new inspections at Spirit, as well as pre-shipment approval requirements on fuselages prior to shipment to Boeing; Added competency assessments for all supplier mechanics doing structural work at Boeing sites; and Issued supplier bulletins to strengthen focus on conformance and reduce the risks of defects being shipped. Key Performance Indicators A significant component of the Product Safety and Quality Plan is the identification of six critical, safety-focused production health KPIs: Employee Proficiency (measures share of employees currently staffed to commercial programs who are proficient); Notice of Escape (NoE) Rework Hours (measures rework due to Fabrication and supplier-provided escapes to Final Assembly); Supplier Shortages (measures Fabrication and supplier shortages/day); Rework Hours per airplane (measures total rework hours per airplane in Final Assembly); Travelers at Factory Rollout (measures jobs traveling from Final Assembly); and Ticketing Performance (measures average escapes per ticketed airplane). Each KPI also has associated control limits and defined criteria that will trigger corrective action and SMS risk monitoring. Product Safety and Quality Plan Attention Areas Safety Management System three main initiatives: Streamlining employee reporting channels; [Submissions are up 500%] Addressing traveled work risk; [implemented a “move ready” process—737 airplanes may not move to the next factory position until identified build milestones are co...